
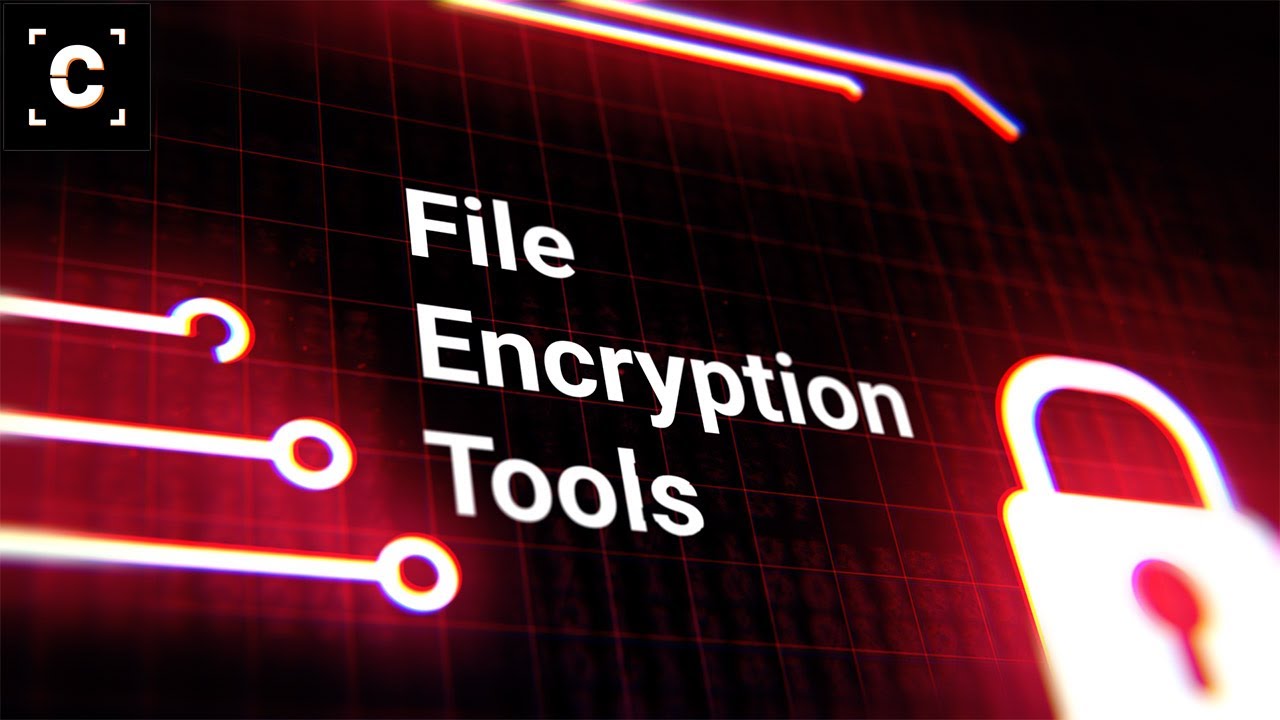
Typical test flow for qualification of a device: Dynamic burn-in with test also allows devices to be tested after the burn-in cycle, eliminating the need to transfer them to a separate tester.

Elimination of these devices significantly improves product quality. Another advantage of burn-in with test is the ability to detect devices that will fail under marginal conditions, but not at the normal operating point. This type of burn-in is especially useful for quickly determining burn-in “fallout” as a function of time, allowing the burn-in process to be terminated at an optimal point. However, dynamic burn-in is limited because it cannot completely simulate what the device would experience during actual use, so all the circuit nodes may not get stressed.ĭynamic Burn-in with test: In this we additionally monitor device outputs at different points in the burn-in process, verifying that the devices are actually being exercised. The advantage of dynamic burn-in is its ability to stress more internal circuits, causing additional failure mechanisms to occur. A major limitation of static burn-in however, is that it exercises fewer than half the circuit nodes on a device.ĭynamic Burn-in: Also referred to as Burn-in for Stress – in this we apply various input stimuli to each device while the device is exposed to extreme temperature and voltage. The advantages of static burn-in are its low cost and simplicity. Static Burn-in: In this we apply extreme voltages and temperatures to each device without operating or exercising the device. With burn-in testing, we stress the device, accelerating these dormant faults to manifest as failures. These faults are dormant and randomly manifest into device failures during device life-cycle. The root cause of fails detected during burn-in testing can be identified as dielectric failures, conductor failures, metallization failures, electromigration, mouse-bites, etc. Traditional stuck-at testing does not detect these types of faults because they may be dormant and need to be stressed to manifest as “fails” (during burn-in). Efficiency of Burn-in test impacted by voltage scaling and power consumption.īurn-in testing detects faults that are generally due to imperfections in manufacturing and packaging processes, which are becoming more common with the increasing circuit complexity and aggressive technology scaling.Non-uniform distribution of stress on device (Inability to put 100% of the device under stress).Mechanical and EOS/ESD damage to parts.Higher cost (Burn-in boards degrade over time and must be replaced).Ability to estimate the product’s useful life period.Delivered product has higher reliability.

Performing burn-in reduces the total life span of a device as shown in the below curve, but it has no impact on the useful life (Stage 2) of a device. (Curve in red shows failure rate due to ageing). These fails are due to critical paths in the device getting worn out. Stage 3: Wear Out/End of Life – Period marked by increase in failure rate due to aging of components this period marks the end of the useful life span of a device.Stage 2: Normal/Useful Life – This is the period where rate of failure is nearly constant, and due to randomly occurring faults.

(Curve in blue shows failure rate due to early fails) During this period components fail at a high rate but this rate decreases with time. These are due to lack of control in manufacturing processes at the molecular level. Stage 1: Infant Mortality/Early Life – This is the period were early failures show up in a component.
